Smart Textiles
Aileen M. Eagleton, Michael Ko, Robert M. Stolz, Nataliia Vereshchuk, & Katherine A. Mirica, Dartmouth College
Dartmouth College researchers have developed a novel method for making electronic textiles using a durable copper-based coating that can be integrated into fabrics. These textiles react to harmful gases in the air and transform them into less toxic substances that become embedded into the fabric.
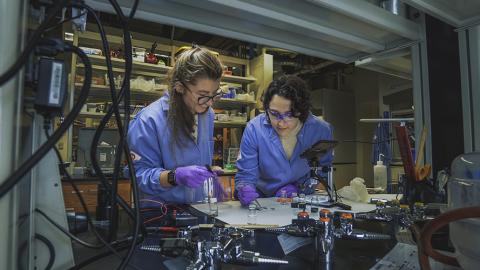
The multi-functional characteristics of these electronic materials (conductivity, porosity, and reactivity) make them ideally suited for chemical sensing, filtration, and decontamination. There are numerous health care, environmental sensing, and personal protection applications for this new discovery.
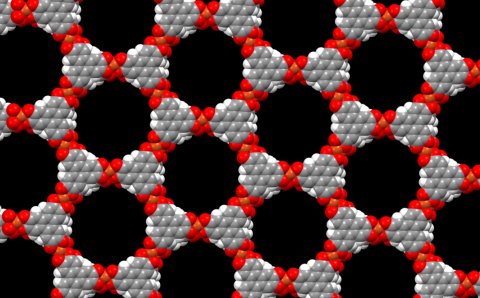
New research results leverage the earlier work of chemists in the Mirica Group at Dartmouth College. Their 2017 study demonstrated the potential of “smart textiles” to detect and transform harmful environmental substances. In that study, Metal Organic Frameworks (MOFs), a conductive matrix of organic ligands interconnected with metallic nodes (image), were treated with a simple coating applied to cotton and polyester fabrics. Further investigations determined that a copper-coated MOF can be precisely integrated into fabrics, allowing researchers to create specific patterns in the material. Repeated testing of these new materials found they converted the toxic gases nitric oxide and hydrogen sulfide into the less harmful gases nitrite, nitrate, and copper sulfide, respectively. These electronic fabrics are also durable and wear-resistant and can be laundered and ironed while maintaining their conductive properties. This durability makes these smart textiles ideally suited for enhanced personal protection equipment and medical applications.
In the future, this new approach might also be used as an economical alternative to technologies that are expensive and limited in where they can be deployed since they require an energy source or rare materials, such as those used in catalytic converters in automobiles.
This study was partially supported by an award to the New Hampshire Center for Multiscale Modeling and Manufacturing of Biomaterials (NH BioMade), an NSF EPSCoR Research Infrastructure Improvement Track-1 project (#1757371), as well as an NSF CAREER award (#1945218). This study has also been featured on the Dartmouth news service and as a EurekAlert.
International Student Exchange Advances Biomaterials Research
Elizabeth Mamros, Jinjin Ha, & Brad Kinsey; UNH
Student exchanges between the University of New Hampshire (UNH) and the Institute of Forming Technology and Lightweight Components (IUL) of the Technical University in Dortmund, Germany led to research advances in biomaterials that would not have been possible without these in-person collaborations.
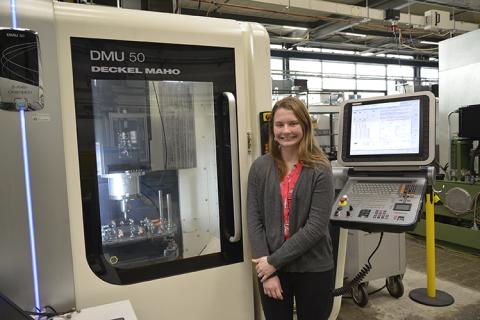
Metallic biomaterials are used to create hardware for trauma fixation applications, such as cranial implants for automobile accident victims or soldiers. To realize the goal of patient-specific hardware in these applications, research is under way on novel sheet metal forming processes to manufacture biomaterials that will have the needed strength, geometry, durability, and biocompatibility.
Elizabeth Mamros, a mechanical engineering PhD candidate at UNH, traveled to Dortmund, Germany in June 2021 for her doctoral research on incremental forming technologies for sheet metal manufacturing processes. Incremental forming is the process whereby a hemispherical tool traverses a clamped piece of sheet metal to locally deform the sheet layer-by-layer. The Institute of Forming Technology and Lightweight Components (IUL) hosted Mamros, who received both a Fulbright and an NSF Graduate International Research Experiences (IIE-GIRE) fellowship to conduct her research in Germany for over one year. IUL faculty provided Mamros with lab support and expertise in using their instrumentation. Unique instruments and process variants that had been developed at the IUL, and were not available in the US, were pivotal to her research.
Upon her return in August 2022, Mamros mentored IUL undergraduate student Lenard Polec at the UNH John Olson Advanced Manufacturing Center. Polec spent the summer learning about incremental forming techniques and continuous bending under tension, using custom built instrumentation available only at the Olson Center. Mamros received funding from the Research Internships in Science and Engineering Worldwide program to support Lenard’s stay at UNH.
These successful student exchanges established a foundation between American and German researchers, paving the way for future student exchanges and new research collaborations. Research discoveries from this work have been published and additional journal manuscripts and conference proceedings are in development. The UNH-IUL collaboration also led to a new collaboration with the National Institute of Standards and Technology (NIST) to further examine one aspect of the formed components. Jinjin Ha, UNH assistant professor of mechanical engineering, traveled to Germany in May 2022 to meet with Mamros and her IUL colleagues, tour their research facilities, and discuss future collaborations. Dr. Ha has since been awarded a Humboldt Foundation fellowship to continue her research on incremental forming and will be hosted by the IUL.
This research was partially supported by an award to the New Hampshire Center for Multiscale Modeling and Manufacturing of Biomaterials (NH BioMade), an NSF EPSCoR Research Infrastructure Improvement Track-1 project (#1757371).
NH Creates
Carmela Amato-Wierda & Amy Booth; UNH
NH CREATES used NH BioMade education seed funds and an NIH (National Institutes of Health) grant to expand 2021 and 2022 summer youth and educator programs into regenerative medicine and biomanufacturing to support workforce development through education. NH CREATES will be sustained with additional $4 million funding as part of a larger $44 million grant awarded to the City of Manchester, NH, and the Advanced Regenerative Manufacturing Institute by the U.S. Economic Development Administration Build Back Better Regional Challenge.
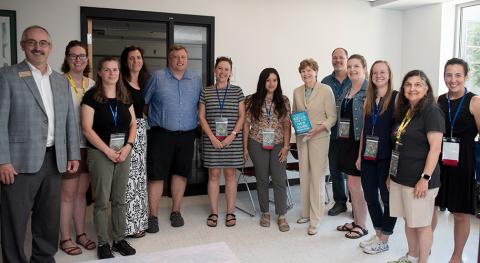
In 2021 and 2022, 89 youth participated in UNH Tech Camp, and 13 teachers participated in a 2-week institute to study regenerative medicine and project-based learning (PBL) instruction. Teachers created critical ongoing relationships with subject matter experts, increased awareness of the biotechnology industry in NH, and began implementation of biotechnology lessons in secondary science classrooms. NH CREATES, building on UNH Tech Camp success, will serve students and teachers in Durham and Manchester in 2023, with a larger pool to recruit individuals from underrepresented groups in Manchester.
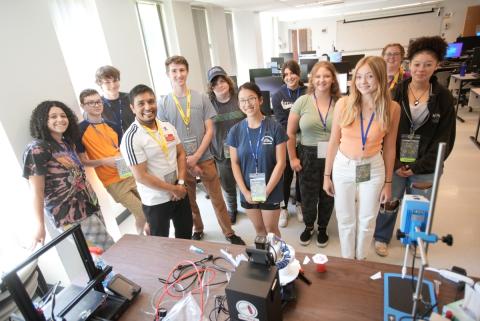
Funds from NH BioMade and NIH worked in tandem to introduce youth and teachers to new biotechnology content at UNH Tech Camp in July 2021 and 2022. University of NH Associate Professor and UNH Tech Camp Director, Carmela Amato-Wierda, designed the Collaborative for Regenerative Medicine Education and Training for Engineers and Scientists of the Future (NH CREATES) to help build a skilled workforce for New Hampshire’s rapidly growing regenerative medicine and biotechnology industries building on UNH Tech Camp success.
UNH Tech Camp held new youth programs focused on topics including bioinformatics, cryopreservation, regeneration with planaria, molecular visualization, 3D bioprinting, and entrepreneurship in biomanufacturing. Students learned topic(s) through hands-on activities in a lab, demonstrations, and lectures. Funds from NH BioMade were used to obtain equipment, such as a 3D bioprinter for the 3D bioprinting youth project.
High school teachers participated in a 2-week institute to study regenerative medicine and project-based learning (PBL) instruction. The teachers (12/13 teachers) developed new curricula and began instruction of biotechnology topics in secondary science classrooms in the fall. Funds from NH BioMade supported teachers’ new classroom equipment, such as microscopes and VR headsets, materials, and guiding institute texts, and one class field trip to Boston University to visit the Gaudette Lab and learn about their efforts using spinach leaves as scaffolds for regenerating heart tissue.
The New Hampshire Center for Multiscale Modeling and Manufacturing of Biomaterials (NH BioMade) is an NSF EPSCoR Research Infrastructure Improvement Track-1 project (#1757371).
NH Climbs Up
Kristen Johnson & Mary Stewart, UNH Manchester
The NH Collaborative Learning through Industry Internships and Academic Mentorship in Biotech for Students Upscaling the Workforce (NH CLIMBS UP), funded by a NH BioMade seed grant, supported workforce development in biomanufacturing. The week-long course provided cell culture skills training through integrated interactions with industry representatives, career and education counselors, and mentors. NH CLIMBS UP cross-trained engineers to understand cell culture and needs of living cells and tissues, a skills gap identified by local industry.
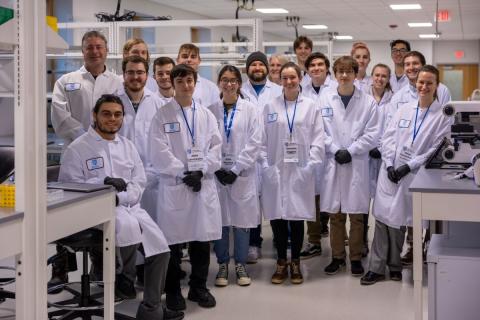
Fifteen participants studied cell passaging, viability assays, cell staining, imaging and wound assay analysis, proper pipetting, and DNA and protein techniques. Evaluations demonstrated a remarkable gain in knowledge by participants. Interest from applicants, industry, and academia indicates the need for wider audiences to access continuing professional development in this topic area. The PIs have plans to repeat the course in 2024.
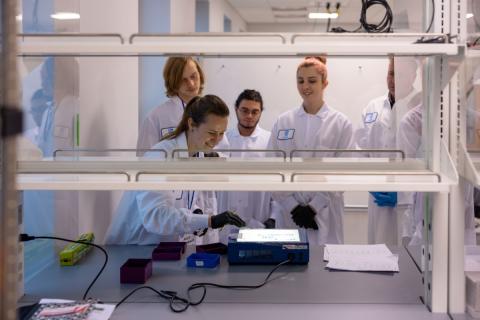
In January 2023, Dr.?Kristen Johnson?and Dr.?Mary Stewart? hosted NH CLIMBS UP at the Biotechnology Innovation Center at University of New Hampshire Manchester to address workforce development needs in biomanufacturing. Engineering and advanced manufacturing students obtained hands-on skills in cell culture and the needs of living cells. Fifteen students were selected from over thirty applicants.The short one-week course piloted a non-credit professional development format. Integration of educational opportunities, coaching, and industry speakers from Eppendorf, Nexcelom, Fisher Scientific, and NovoNordisk made the course unique. UNH graduates offered career guidance support to participants. In addition to the lab training and mentorship, participants toured the Advanced Regenerative Manufacturing Institute (ARMI) labs and received resume and networking guidance from UNH Career and Professional Services.
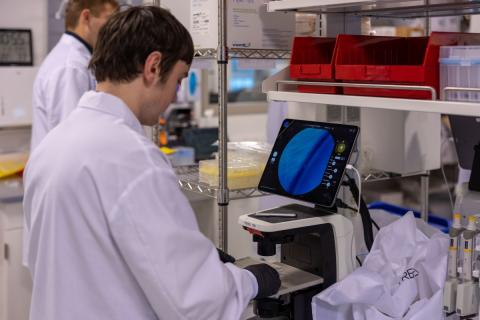
As one respondent to the evaluation survey said:
This was a strong intro to cell culture and did a good job of expanding my knowledge of biology. [The instructors] were knowledgeable and approachable instructors. They were able to make me more comfortable with something I had no prior experience with in an incredibly short time. One thing I'd like to see in future expansions is the use of bioreactors, because they seem very important to the industry, and I'm interested in learning the basics of operating one.
The New Hampshire Center for Multiscale Modeling and Manufacturing of Biomaterials (NH BioMade) is an NSF EPSCoR Research Infrastructure Improvement Track-1 project (#1757371).
Closing in on Chronic Wound Treatment
Kyung Jae Jeong & Young Jo Kim; UNH
University of New Hampshire EPSCoR researchers have been awarded a three-year, $600,000 National Institutes of Health (NIH) grant to further their work developing an injectable treatment for chronic wounds that uses gelatin combined with melanin?extracted from cuttlefish, a marine invertebrate. The foundation for this research was established through a seed funding grant from NH BioMade.
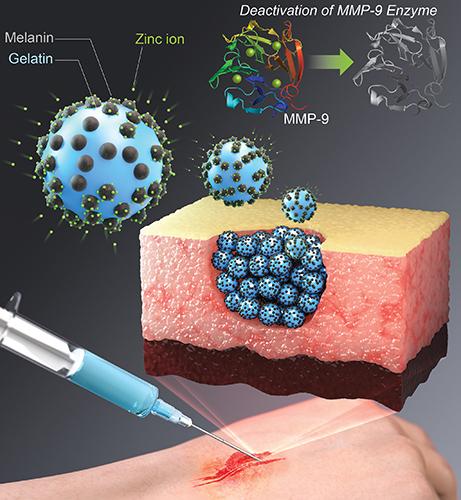
An estimated 6.5 million Americans experience wounds that do not heal properly, the result of severe trauma and health conditions such as diabetes and obesity. Without proper healing, wounds can remain infected and worsen, leading to tissue gangrene, amputation, and even death.
The enzyme matrix metalloproteinases (MMP-9) plays a pivotal role in delaying wound healing, yet the use of MMP inhibitors have resulted in adverse side effects such as musculoskeletal pain. UNH chemical engineering faculty Kyung Jae Jeong and?Young Jo Kim are investigating a novel approach to deactivating MMP-9 through use of an injectable hydrogel treatment formed by synthesizing gelatin with melanin derived from cuttlefish ink sacs. Applied to the affected wound, this hydrogel deactivates the enzyme by absorbing zinc ions from MMP-9.
The goal of their NIH-funded study is to create a cost-effective and biocompatible wound?treatment option and may also lead to new treatment options for other MMP-associated diseases, such as ocular inflammatory diseases and metastatic cancer.
Thee “Trailblazer” award from NIH (R21EB032134) builds on their prior research examining melanin pigments extracted from horsehair, funded by a seed funding grant from the New Hampshire Center for Multiscale Modeling and Manufacturing of Biomaterials (NH BioMade), an NSF EPSCoR Research Infrastructure Improvement Track-1 project (#1757371).
Undergraduates Shine in Collaborative Biomaterials Research Study
Md. Ahasan Habib, James Kraly, and Lisa Hix; Keene State College
With support from both the National Science Foundation’s Established Program to Stimulate Competitive Research (EPSCoR) and the National Institutes of Health’s IDeA Network of Biomedical Research Excellence (INBRE) programs, undergraduate students at Keene State College are gaining valuable research opportunities not typically available to students at this Primarily Undergraduate Institution (PUI).

Students have developed core competencies in mathematics, Computer Aided Design, biomaterials research, and scientific writing, and are making noteworthy contributions to the field of tissue engineering. Their contributions will support the foundation of many regenerative medicine advances on the horizon, such as 3D printed organ transplants.
Undergraduate students Slesha Tuladhar, Carter Nelson, Connor Quigley, and Amar Abbatiello are research assistants of Dr. Md. Ahasan Habib in the Additive Biomanufacturing Lab at Keene State College. Students are testing materials to determine which are easily printable, favorable to living cells, and structurally supportive in larger scaffolds or organ tissues. They are also testing cell cultures. These students have become lead authors of peer-reviewed journal articles and conference proceedings, and presented their results at scientific conferences and to graduate students and faculty members at the University of New Hampshire and Dartmouth College.
Because these students are part of the tissue engineering research thrust of the New Hampshire Center for Multiscale Modeling and Manufacturing of Biomaterials (NH BioMade), they’ve gained insights into a large, statewide, collaborative, and multidisciplinary research program; have had professional development opportunities; and are working alongside the research faculty and graduate students at both UNH and Dartmouth. They are well positioned for either graduate school or career opportunities in New Hampshire’s emerging biomaterials industry.
The Keene State College students are also spotlighted in this article, Cutting-edge biomaterials research part of undergraduate experience at KSC.
This research was partially supported by an award to the New Hampshire Center for Multiscale Modeling and Manufacturing of Biomaterials (NH BioMade), an NSF EPSCoR Research Infrastructure Improvement Track-1 project (#1757371)
New Biotechnology Course Supports New Hampshire’s Biomanufacturing Ecosystem
Kyle Plante; Pinkerton Academy
A new high school course in introductory biotechnology was developed with support from a seed funding grant from NH BioMade, an NSF EPSCoR Track-1 project led by the University of New Hampshire. Such grants to K-12 teachers and community college faculty for course development are one component of the NH BioMade seed funding program.
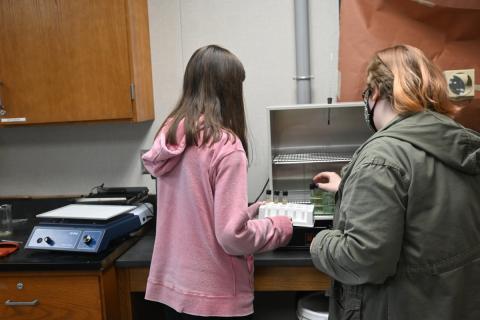
New Hampshire has a growing biotechnology industry, but employers are having difficulty finding trained workers. Expanding this capacity is a key objective of NH BioMade. The new high school course was developed as a model for other high schools and community colleges and to create a diverse workforce pipeline.
Kyle Plante, a high school science teacher at Pinkerton Academy in Derry, NH, created an Introduction to Biotechnology course in 2021 with seed funding from the New Hampshire Center for Multiscale Modeling and Manufacturing of Biomaterials (NH BioMade). The course was developed around four quality performance assessments (QPAs), which are central topics in biotechnology: 1) biochemistry, 2) cell culture, 3) genetic transformation, and 4) a practical application of a societal problem that lends itself to bioengineering solutions. Thirty-two students successfully completed the class this year; 21 identified as female and nine are from underrepresented minorities.
Based on student feedback and requests to have more time to work on their experiments, the Introduction to Biotechnology course was a success and is being redesigned for the 2022-23 academic year as a semester-long class that meets every day. Forty students are scheduled to take the course next year. In response to student requests, a Biotechnology II course is under review at the high school, as well as potential partners at community colleges and other higher education institutions.
NH BioMade is an NSF EPSCoR Research Infrastructure Improvement Track-1 project (#1757371).
Mechanically Adaptive 3D Printing Materials that can React to External Stimuli Has Potential Use in Soft Robotics
Chenfeng Ke, Dartmouth College
A team of chemists has developed a series of mechanically adaptive 3D printing hydrogels that dynamically change their stiffness, from soft rubbery states to hard plastic states. These hydrogels will enable the design and fabrication of sophisticated soft robots.
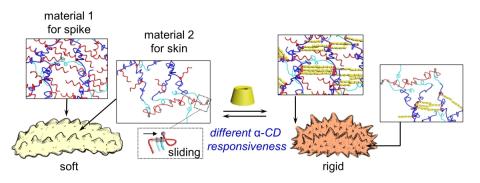
Instrumentation and Equipment Portal Helps Connect Resources with Research Needs
Shawn Banker & Justine Stadler, UNH
The NH Research Asset Portal provides a publicly accessible, centralized website to search for and request use of advanced laboratory instruments, equipment and expertise to support academic and industrial research. In addition, grants are available to access instruments for biomaterials research.
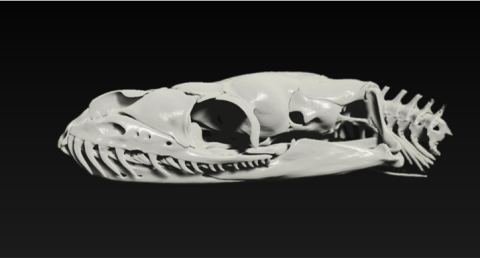
The NH Research Asset Portal enhances the connection between the state’s research universities, where the equipment resides, with primarily undergraduate institutions and industry partners by providing access to research resources. This will increase the utilization of high-end instrumentation and minimize duplication through collaborative applications and remote-use capabilities.
The NH BioMade Core Facilities Team created the NH Research Asset Portal, which lists key instrumentation, equipment, and research expertise at Dartmouth College and the University of New Hampshire, in order to expand access to users outside of these research institutions. The portal provides information about instrumentation and equipment and contacts of personnel who can assist users gain access and operate the equipment, and it provides a searchable database to research expertise at UNH and Dartmouth. The NH Research Asset Portal has capacity to include research assets from other institutions and increase access and use by academic scientists, research and development companies, manufacturers and start-ups.
The NH Research Asset Portal was partially supported by an award to the New Hampshire Center for Multiscale Modeling and Manufacturing of Biomaterials (NH BioMade), an NSF EPSCoR Research Infrastructure Improvement Track-1 project (#1757371).
Employing Conductive Metal-Organic Frameworks for Electrochemical Detection of Neurochemicals
Katherine Mirica, Dartmouth College
A team of chemists at Dartmouth College has demonstrated a novel technological approach for the detection of neurochemicals in aqueous solutions, an important tool in medicine to assess stress and exertion, providing early diagnosis, treating disorders, and modifying human behavior.
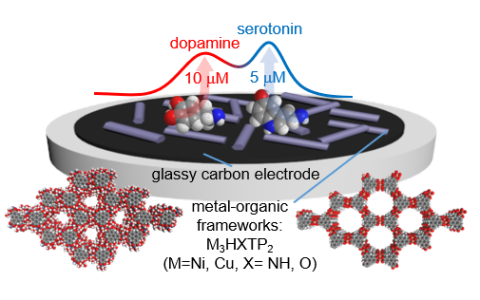
This approach, published in the Journal of the American Chemical Society, uses two-dimensional, conductive metal-organic frameworks (MOF) which are broadly applicable and synthetically accessible, and could advance the field of electrochemical sensors in multifunctional and stable sensing devices and, ultimately, in sensitive arrays to detect neurochemicals in biological systems.
Electrochemical detection of neurochemicals such as dopamine, serotonin, ascorbic acid, and uric acid, which have significant roles in human physiology, is important for the early diagnosis and treatment of health disorders. Although breakthroughs in designs of materials and devices have led to advances in rapid detection and continuous monitoring of neurochemicals, major challenges currently inhibit progress toward technological applications.
This study demonstrates the novel use of two-dimensional (2D) conductive metal-organic frameworks (MOFs) as mediators in the detection of these neurochemicals in aqueous solutions such as urine. This approach merges a unique class of chemically precise materials with the ease of synthetic access with no further chemical modifications, high sensitivity and selectivity in sensing, and easy device integration. The implementation of 2D MOFs in clinical applications may have potential use for disease diagnostics, tumor detection, and monitoring of drug delivery for Parkinson’s disease and depression.
This research was partially supported by an award to the New Hampshire Center for Multiscale Modeling and Manufacturing of Biomaterials (NH BioMade), an NSF EPSCoR Research Infrastructure Improvement Track-1 project (#1757371).
NH BioMade Helps Community College Students Transfer to Four-Year Programs
Steve Hale and Allison Wasiewski, UNH
To improve the recruitment and retention of underrepresented groups in biomaterials and advanced manufacturing in New Hampshire, the NH BioMade Transfer Scholars program was created to support community college students interested in attaining a four-year degree in a NH BioMade-related discipline. Six students were supported in the 2019 – 2020 academic year.
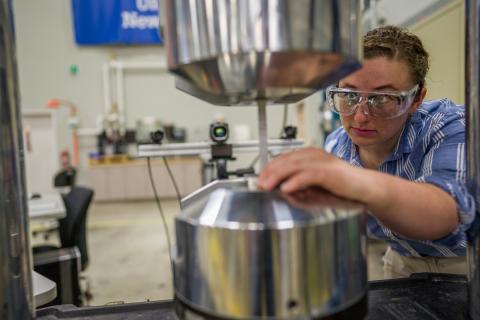
Community colleges serve a diverse student population. The NH BioMade Transfer Scholars program, an integral component of this NSF EPSCoR project’s education and workforce development initiatives, was able to support six students from underrepresented groups transition from community college to four-year institutions.
The NH BioMade Transfer Scholars Program provides financial and mentorship support to four female students at the University of New Hampshire in Durham (one bioengineering major, three mechanical engineering majors) and to two female students at the University of New Hampshire in Manchester (biotechnology majors). All six are from underrepresented groups and participated in mentorship activities. The overall grade point average of these students after their first semester was a 3.7, demonstrating that community college students can be academically prepared to be competitive at four-year universities.
Outreach activities performed by the scholars is another key component to the program. These students visited Great Bay Community College, Manchester Community College, Nashua Community College, and NHTI-Concord’s Community College to recruit diverse students for NH BioMade education and workforce development programs. Scholars presented the programs and their experiences to over 120 students from different Community Colleges in NH.
Since the program's inception in 2019, 13 female community college students (54% of all transfer scholars) have become NH BioMade Transfer Scholars. Ten have graduated, receiving their bachelor's degrees in STEM disciplines. Two female students are currently transfer scholars and are pursuing their 4-year degrees. Graduated students have gone on to pursue advanced degrees and are working as engineers and bioscientists. One former transfer scholar is a NH high school mathematics teacher.
This program is made possible by an award to the New Hampshire Center for Multiscale Modeling and Manufacturing of Biomaterials (NH BioMade), an NSF EPSCoR Research Infrastructure Improvement Track-1 project (#1757371).
Industry Partnership Leads to Senior Capstone Project
Russell Carr and John Tsavalas, UNH
Students at the University of New Hampshire used equipment funded by NH BioMade to complete their senior capstone project. NH BioMade industry partner Advanced Solutions Life Sciences worked with faculty and students to help them gain experience in the use of the company’s BioAssemblyBot, a 3D human tissue printer that operates on a six-axis robot.
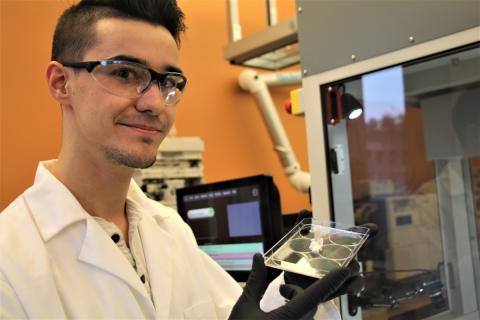
Two BioAssemblyBots acquired for the University of New Hampshire and Dartmouth College are now available for use by students and faculty at other New Hampshire colleges and industry partners.
The NH BioMade project, funded by NSF EPSCoR, is forging a connection between the state’s research universities, primarily undergraduate institutions, and industry partners. Through these new connections, NH BioMade acquired two BioAssemblyBots from Advanced Solutions Life Sciences in Manchester, NH. The BioAssembyBot is a six-axis robotic printer that is able to fabricate biological tissues for research.
When a UNH student group learned that the BioAssemblyBot had been installed on campus, a senior capstone project was designed to develop an assay technique to measure cell viability in 3D constructs. Chemical engineering faculty at the University of New Hampshire introduced these students to NH BioMade faculty and to the industry partner and they learned how to use the equipment at the industry site. The students were then able to bring their new knowledge and skills back to campus to use the equipment there. This experience has a paved a pathway for New Hampshire students, faculty, and industry partners to have valuable interactions.
NH BioMade is an NSF EPSCoR Research Infrastructure Improvement Track-1 project (#1757371).